Prozessautomatisierung
Revolutionierung der Glasverarbeitung durch Automatisierung
In der glasverarbeitenden Industrie ist Automatisierung die Zukunft.
Hier sind drei Möglichkeiten, wie die Prozessautomatisierung von Glaston die Karten neu mischt.
1.
VERBESSERTE ARBEITSEFFIZIENZ UND SICHERHEIT AM ARBEITSPLATZ
- Vereinfachte Bedienung mit einem Minimum an Bedienereingriffen
- Intelligente, benutzerfreundliche Prozessintelligenz
- Zukunftssichere Prozesse mit Glastons Innovationen und Dienstleistungen
2.
MEHR KONSISTENZ UND ENERGIEEINSPARUNGEN
- Zuverlässiger und wiederholbarer Ladungsdurchsatz
- Optimierte Prozessschritte im gesamten Betriebsablauf
- Energieeffizientes Be- und Entladen
3.
HÖCHSTE QUALITÄT, KAPAZITÄT ODER BEIDES
- Optimierte Glasqualität und -konsistenz
- Erhöhte Effizienz, Leistung und Produktionsleistung
- Maximale Flexibilität zur Anpassung an Ihre Prozessziele
Innovative Automatisierungslösungen, die Ihren Anforderungen entsprechen
Glaston Prozessautomatisierung ist die Antwort auf den weltweiten Ruf der Glasverarbeitungsindustrie nach mehr automatisierten und intelligenten Abläufen. Durch die Kombination von mechanischer Automatisierung und Prozessintelligenz wird sichergestellt, dass jeder Schritt in Ihrer Glasverarbeitung nicht nur automatisiert, sondern auch auf optimale Weise ausgeführt wird – immer.
Der Grund, warum wir mit der Entwicklung von Prozessautomatisierung begonnen haben, ist, dass wir wissen, wie schwierig es ist, Personal für Routinearbeiten in der Glasverarbeitung zu finden, zu schulen und zu halten. Durch die Automatisierung bestimmter Prozesse kann Ihr Bedienpersonal für attraktivere und wertschöpfendere Aufgaben eingesetzt werden.
Würde Ihnen die Prozessautomatisierung nützen? Machen Sie dieses kurze Quiz, um es herauszufinden!
Umgekehrte Automatisierung für Glasqualität auf Weltklasseniveau
Wir haben unsere Reise mit der Automatisierung von innen nach außen begonnen – angefangen mit unserem umfassenden Wissen über die Kernprozesse, das uns die besten Möglichkeiten zur Automatisierung von Glasproduktionslinien bietet. Darin liegt unserer Meinung nach das Geheimnis einer Glasproduktion von erstklassiger Qualität.
Aufbauend auf dem bewährten Prozess-Know-how und Fachwissen setzt die Glaston Prozessautomatisierung modernste Technologien ein, um die Qualität der Endprodukte zu verbessern und die Kapazität, Energieeffizienz und Sicherheit des Bedienpersonals zu erhöhen.
SERIENPRODUKTION
Eine der typischsten Anwendungen der Automatisierung in der Glasverarbeitung sind große Serienfertigungslinien, die in der Regel zur Herstellung von vorgespannten Glasprodukten für Möbel, Haushaltsgeräte sowie Duschtüren oder -fenstern in Standardgröße eingesetzt werden. Die Automatisierung ist ideal für die Produktion von begrenzten Größenvariationen und kleinen bis mittleren Glasgrößen.
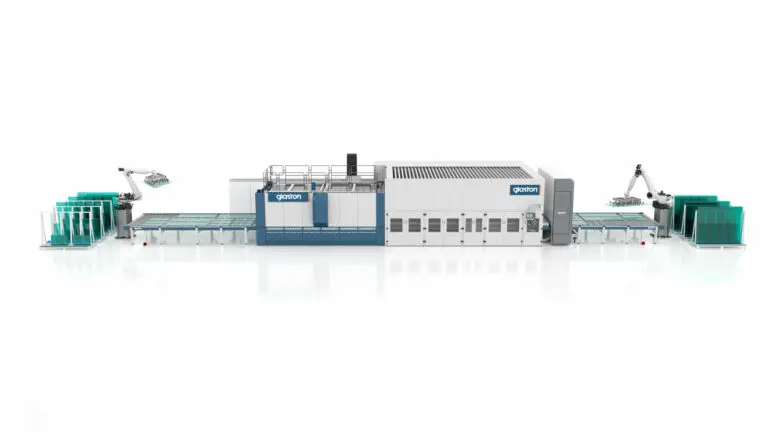
GEMISCHTE PRODUKTION
Die Automatisierung kann auch bei der gemischten Produktion oder bei eigenständigen Anlagen zur Handhabung unterschiedlicher Glasarten und -größen erhebliche Vorteile bringen. Unsere Automatisierung zur Optimierung der Chargenbildung ist für jeden Verarbeiter mit stark schwankenden Produktionsanforderungen verfügbar. Die robotergestützte Beladung kann die Chargenbeladung effizient optimieren und mit einer Vielzahl von Glasdicken und -größen arbeiten. Mithilfe der Automatisierung können potenziell bis zu 70–90 % der Aufgaben in der gemischten Produktion abgedeckt werden, sodass die verbleibenden speziellen übergroßen Gläser manuell bearbeitet werden können.
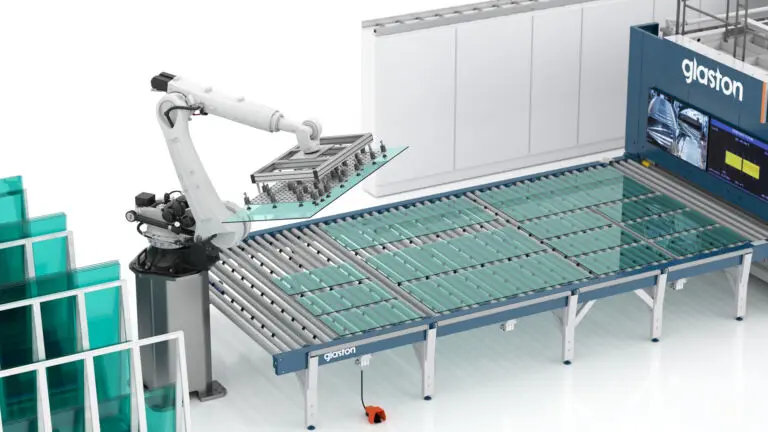
LÖSUNGEN
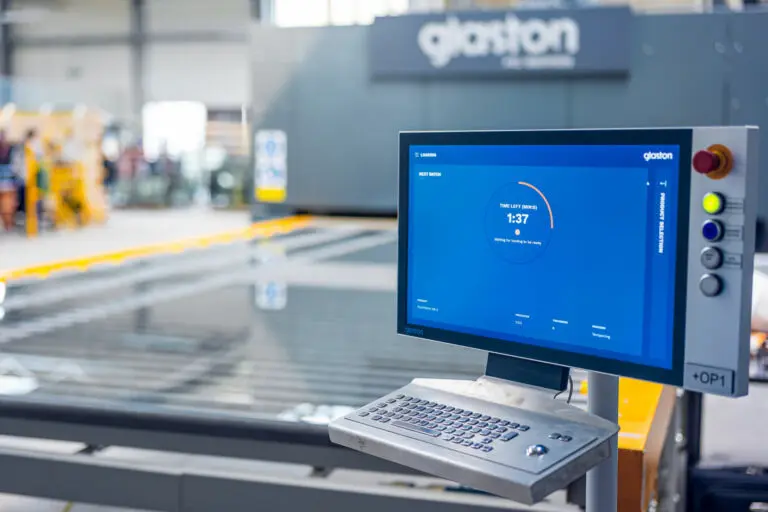
Glaston Autopilot, unser Vorzeigeprodukt für die Automatisierung von Glasvorspannanlagen, ist ein hervorragendes Beispiel dafür, wie wir das Vorspannen von Glas durch intelligente Automatisierung neu gestalten. Autopilot reduziert den Bedarf an manuellen Eingriffen, indem es eine Prozesssteuerung ohne Parameter bietet. Es stellt automatisch alle erforderlichen Parameter basierend auf der Platzierung der Glasscheibe auf der Linie ein, sodass das Bedienpersonal den Prozess einfach überwachen kann.
Lesen Sie, was Anwender über den Autopilot im Vorspannprozess sagen.
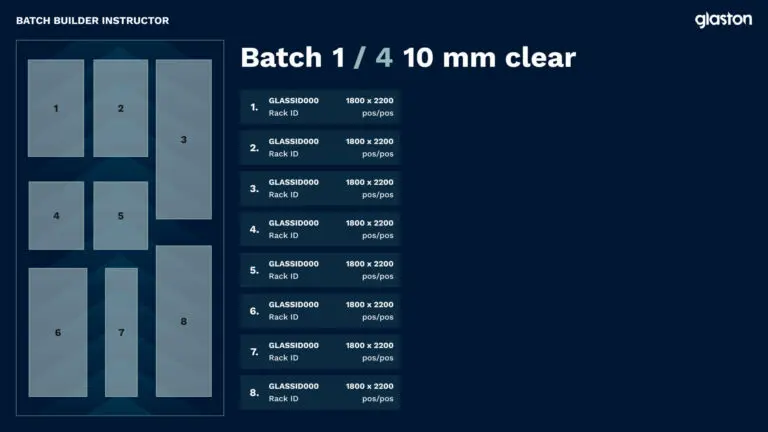
Batch Building Instructor für effizientes Beladen des Ofens
- Effizientere Beladung – höhere Kapazität und Energieeinsparungen
- Vorspannprozess im Kern – beste Qualität der Endprodukte
- Prozessablauf im Voraus bekannt – verbesserte Vorteile durch Produktionssteuerung
Systembeschreibung
- Basierend auf den Anforderungen des Vorspannprozesses wird das Bedienpersonal bei der Positionierung der Gläser auf dem Ladetisch angeleitet
- Glasinformationen werden über eine Verbindung zu einer Produktionssteuerungssoftware gesammelt und die Positionen der Glasscheiben in den Gestellen übermittelt
- Kann in Verbindung mit jedem Glaston- oder Tamglass-Ofen installiert werden
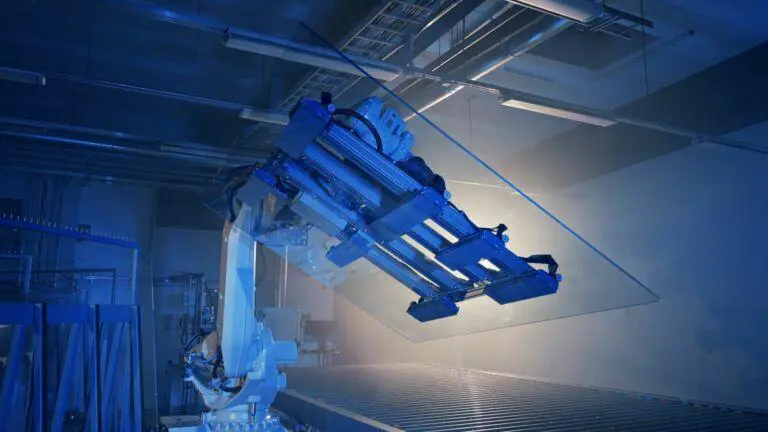
Vollautomatisches Ladesystem für Öfen zum Vorspannen von Flachglas. Es kann von Glasgestellen oder Förderbändern beladen werden. Die Nutzung des Ladebetts und die ofenspezifischen Prozessparameter werden durch spezielle, von Glaston entwickelte Algorithmen eingestellt.
- Automatisches Beladen von Glasgestellen mit einem Roboter – offensichtliche Vorteile in Bezug auf Arbeitsaufwand und Qualität
- Batch-Erstellung mit dem Glaston Batch Master – maximale Effizienz und Energieeinsparungen
- Verbindung zur Produktionssteuerungssoftware – weitere Vorteile bei der Produktionssteuerung
Systembeschreibung
- Armroboter mit servogesteuertem Vakuumgreifer für verschiedene Glasgrößen
- Spezielle Glasgestellpositionen in Reichweite des Roboters
- Batch-Erstellung durch den Glaston Batch Master
- Kann an jedem Glaston- oder Tamglass-Ofen installiert werden
- Komplettlieferung mit Anschlüssen und Sicherheitsfunktionen