When the glasstec trade fair opens its doors in Düsseldorf on 23-26 October 2018, Bystronic glass will present innovations and trends in architectural, automotive and display glass manufacturing in Hall 14 at Stand A51/A52 true to the motto “Join us at the top“. This exhibition motto will be taken in a proverbial sense because visitors of the Bystronic glass booth are awaiting an unique “sporting challenge”. What kind of event highlight it is all about, this secret we won’t be giving away now.
Bystronic glass will present more than 50 years of experience in innovative glass processing solutions for the architectural, automotive and display glass industries in over 1,000 sqm of exhibition space. A number of moderated, live machinery presentations will take place every day to provide the visitors with an in-depth view of the fascinating technologies. Cooperation partner HEGLA will again be on the neighbouring stand, enabling the customers to easily enter into discussions with experts from both of the companies.
I.G. unit sealing in maxi sizes
The Bystronic glass sealing robot jumbo’sealer is a solution for efficient I.G. unit sealing in maxi sizes. The core is its dynamic mixing system. In contrast to the static mixing system that is very common in the sector, the dynamic mixer works with a significantly reduced material pressure. With a flow rate of up to six litres per minute, it also makes the utmost material volume available. As a result, the jumbo‘sealer is able to seal even deep spacer setbacks of rectangular units compared to other machines in the market. With the XXL version, glass sizes up to 18 m in length at a total weight of up to 10 tons can be sealed – and this for up to 4-sided stepped I.G. units.
What also sets it apart from other sealing robots in the glass industry is its automatic material changing system that allows operator-free changing of the sealing material – from polysulphide to silicone for instance – inside two minutes. Furthermore, there are several undergripping options in the discharge area that support the removal of the fully sealed Jumbo units.
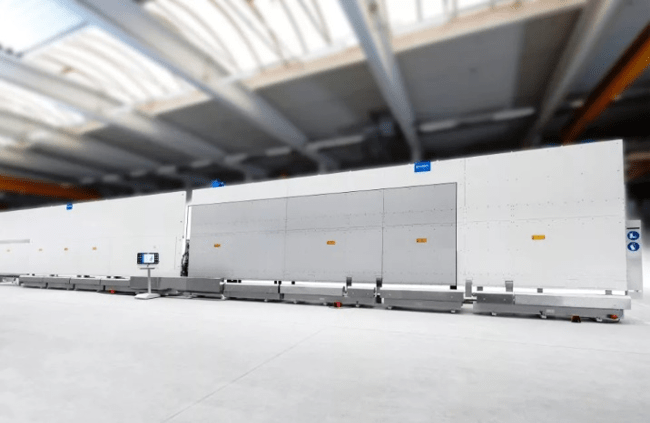
Architectural Glass – TPS® the original from the inventor
TPS® stands for Thermo Plastic Spacer. Bystronic glass is the inventor of this «warm edge» technology and launched this system in 1994. This is the ORIGINAL with much more than 100 installed TPS® I.G. lines worldwide.
A big advantage of TPS® is the production flexibility: The change of the spacer widths between the lites is fully-automatic meaning that no operator intervention is required whatsoever. The respectively required spacer is applied directly to the glass plate – no separate pre-production or provision of suitable spacers is required. The material comes from the drum and is applied as a bead in a proven process. The gas-tight bevel joint that has been proven repeatedly does not require any thermal-mechanical reworking.
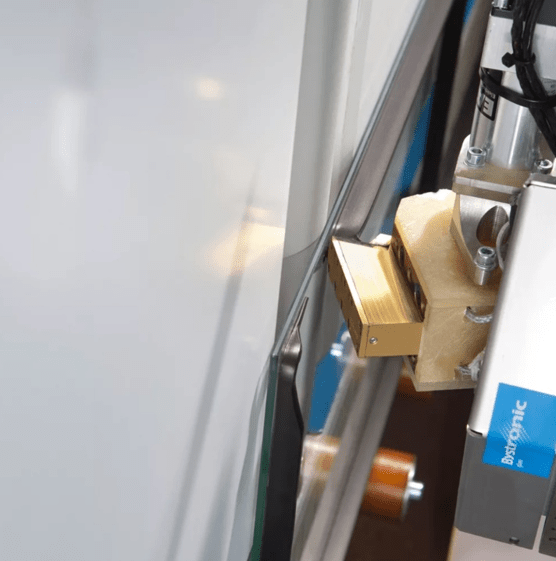
Flexible spacer frame production of warm edge spacers
A further new product of Bystronic glass is the spacerbender MULTI, an economical solution especially for bending warm edge spacer profiles with heated corners. Besides these products aluminum- and warm edge hybrid profiles can be processed automatically. Its flexibility underlines the spacerbender MULTI by the fact, that there are no tool modifications for the processing of different spacer types, spacer thicknesses and colours requested.
Additionally thanks to its user-friendly guidance the spacerbender MULTI is impressive with its perfectly formed and radius-free 90° heated corner of warm edge spacers. This proven technology is based on a patent of the company Lombarda Macchine S.A.S. Furthermore the machine wins over its modern design that has been styled by the renowned DESIGNPF – School of Design in Pforzheim (Germany).
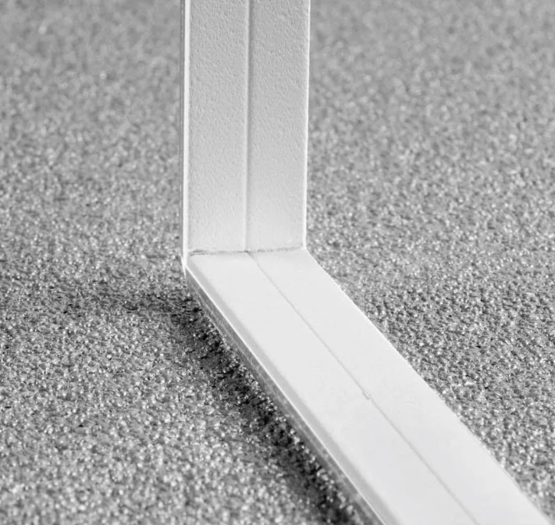
Glass handling – customers remain flexible
With B’VACOOM Bystronic glass will present a completely new generation of handling equipment for efficient flat glass and plate processing. This new developed machine generation represents a successful combination of traditional equipment manufacturing and digital transformation, let’s call it Bystronic glass 4.0 in practical use.
The integrated load control ensures that just the appropriate maximum weight may be lifted. By means of the automatic vacuum control the suction cups are displaying eventual vacuum losses and switch off immediately if the vacuum for the requested weight won’t be available anymore. Additionally predictive maintenance will be possible with the new B’VACOOM generation. Integrated sensors intelligently signal the essential change of the suction cups or other components for the vacuum generation.
The ergonomic design and the proven rigid guidance require minimum effort for the operator and the new designed touch display offers simple machine operation and numerous analysis tools, e.g. the daily output. Increased safety offers among others the password protection of the B’VACOOM handling devices against unauthorized use.
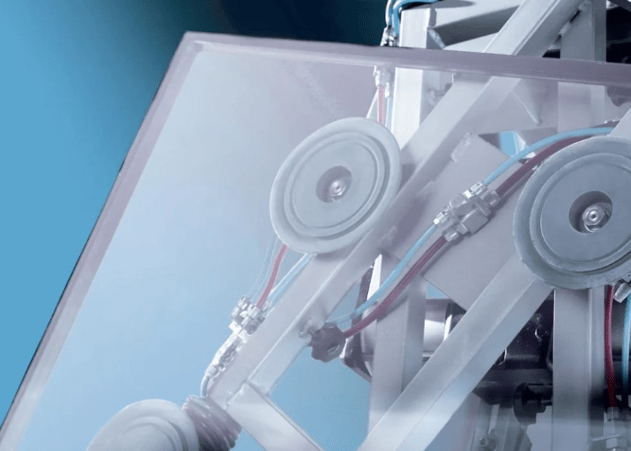
Efficient manufacturing of automotive and display glass
Profitability in automotive glass and display glass processing will now be redefined. At glasstec 2018 Bystronic glass will present the B‘CHAMP WS, a complete cell for the pre-processing of windshields. B’CHAMP installations enable fast and precise cutting, breaking, grinding and drilling of automotive or display glass down to 0.4. mm glass thickness.
By optimising the key components for the glass processing in a linear manner, space is saved through ingenuity. This leads to a reduced footprint of up to 50 %, a transparent and continuous material flow as well as a simple installation and improved maintenance possibilities. The improved accessibility to the key components and the innovative software-based support dramatically improves changeover times. For glass producers this means shorter changeover times when changing the model, simplified maintenance and highest possible flexibility in connection with the automated single piece production.
Due to the modular design of the B’CHAMP, it enables to combine several cells together or add additional components that are individually adapted to the customers’ specific requirements – from glass loading, to primitive cutting, through to finished pre-processed automotive or display glass – all in one system.
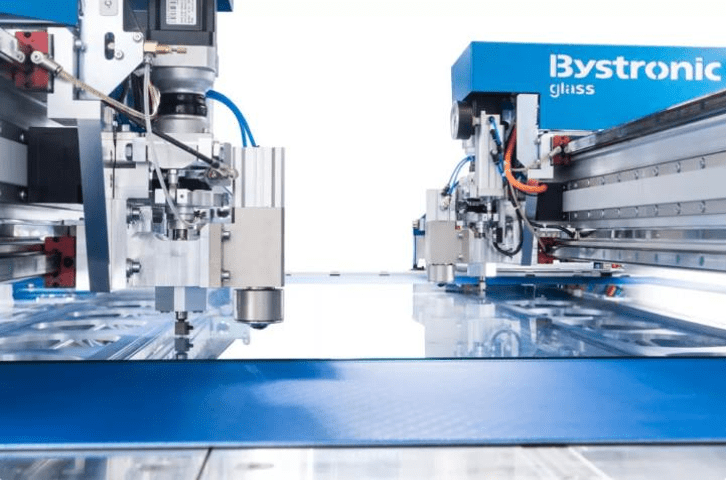
Bystronic glass 4.0 – customers look to the future
In the future everything will be more closely connected: machines, data, processes and applications. Bystronic glass connects all of these modules within the process chain by means of integrated data management – therefore providing customers with considerable competitive advantages. All of the measures, services, products and business models are aimed at securing quality in the final products, increasing the availability of the plants, and shortening process times, which ultimately result in reduced costs and increased revenues. How this Bystronic glass 4.0 works, glasstec visitors are able to discover at a concrete example at the Bystronic glass stand.
Lecture at International Conference – Function meets Glass
Being a part of the International Conference «Function meets Glass» Bystronic glass will hold a lecture on Monday, 22nd October 2018 at 4.30 p.m. entitled «High efficiency in thin glass manufacturing – from glass cutting to edge processing».
Dr. Robert Prange (Managing Director Bystronic Maschinen AG, Bützberg/CH) will give a comprehensive overview about the different fields of application in thin glass processing and the coherent requirements of the technical equipment.