Environmental impact
Own operations
Glaston’s environmental work is driven by the company’s environmental and climate change policy, which defines a commitment to systematic reduction of environmental loading. Download the Policy here.
Glaston’s own operations, which mainly consist of the assembly of glass processing machinery, do not pose a significant risk of air, water or soil pollution. In the company’s activities, Glaston’s most significant environmental impacts arise from energy consumption and related emissions.
At Glaston’s assembly and production units, we operate in accordance with the ISO 9001 quality management system. In Finland, Glaston manages environmental issues in accordance with the ISO 14001 environmental management system.
Reducing emissions of own operations
In 2023, emissions from Glaston’s own operations totaled 1,238 tCO2 i (1,491 tCO2 in 2022), of which fuels and natural gas (Scope 1) account for around 45% and electricity and district heat (Scope 2) for around 55%.
Emissions in the value chain
Scope 1 and 2 emissions from Glaston’s own operations represent a small fraction of Glaston’s total emissions. The majority, above 99%, of all emissions associated with Glaston’s activities arise in the company’s value chain (Scope 3). The most significant sources of emissions are the electricity consumed during the life cycle of the machines manufactured by Glaston (81%) and emissions arising from purchased products and services (17%). In 2023, the Scope 3 emissions totaled 322,644 tCO2 (684,150 tCO2 in 2022).
Glaston’s annual Scope 3 emissions are significantly affected by the type of glass processing solutions that customers purchase. Glaston supplies its customers with different machines in different years, which is why absolute Scope 3 emissions fluctuate from year to year.
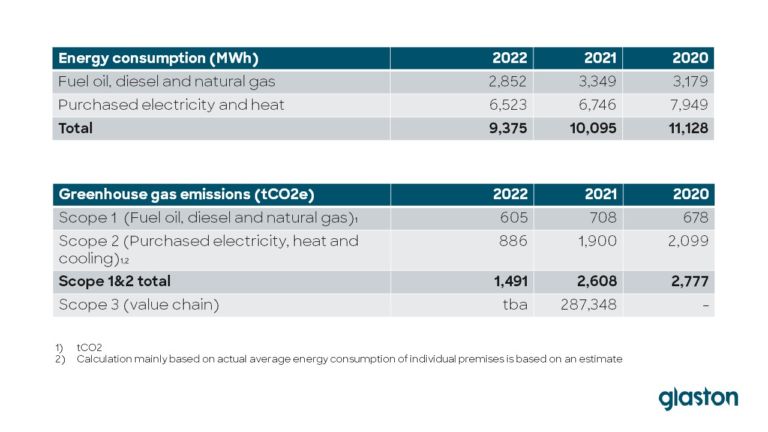
Recycling of packaging materials and waste
The primary aim is to prevent the generation of waste. The goal is to minimize the amount of waste in general, and particularly the amount that ends up other than in final disposal. Glaston’s operations give rise to a lot of packaging materials, and they are sorted and either recycled or used as energy waste. In 2023, the total amount of waste decreased. However, the relative amount of landfill waste increased due to the increased production volume of the Chinese factory.
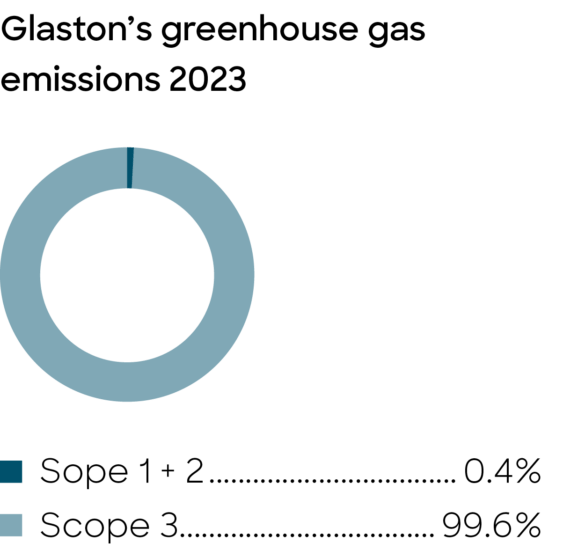
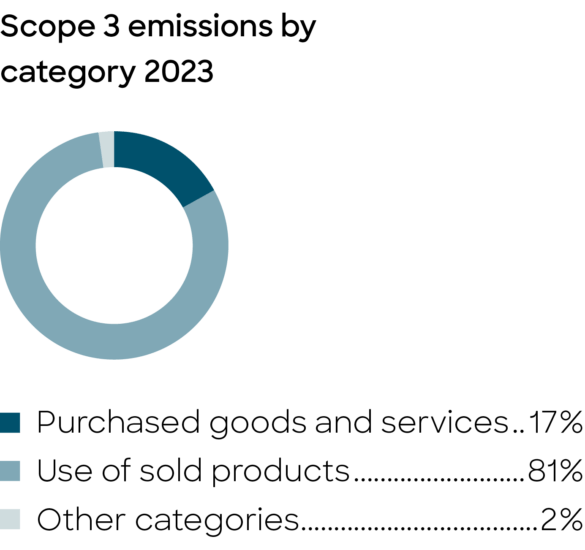
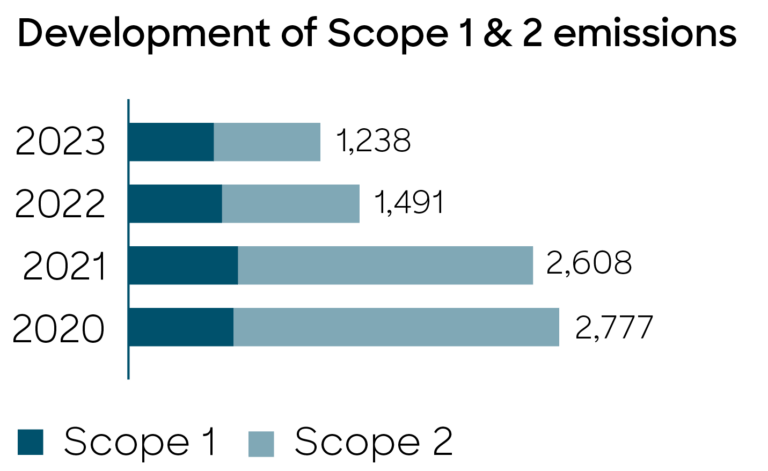
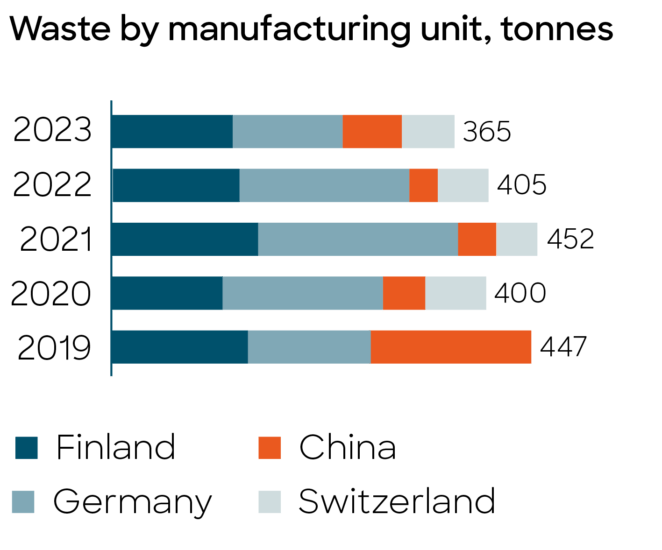
Energy-efficient technology
In Glaston’s operations, the most significant environmental impacts arise when customers use machines purchased from us.
The operating life of Glaston’s tempering machines is fairly long. A significant part of the operating costs of the machines comes from the price of energy. Our product development has therefore long focused on improving the energy-efficiency of the machines. As a result of this work, we have been able to substantially reduce the energy consumption of the most significant products in our tempering machine portfolio. For example, in the tempering process of low-emissivity glass, energy consumption has been reduced by around 30% over the last decade.
Electricity consumption in the manufacturing of glass pre-processing machines and insulating glass units is low and, as a result of product development, consumption has been reduced even further. Development has focused on, for example, conveyor control and optimization of washing machine ventilation.
In product development, we utilize new technology and the opportunities created by digitalization. With the aid of cloud services and the industrial internet, the we help our customers to use their machines as efficiently as possible. A real-time quality measurement system detects deviations in the quality of processed glass immediately, thereby minimizing material waste.
Our machines are designed to withstand constant use at high utilization rates. At Glaston, we pay special attention to the quality and durability of the materials used in the machines. Our production and assembly processes and installation methods are designed to promote product quality and reliability as well as the safety of installers and customers.
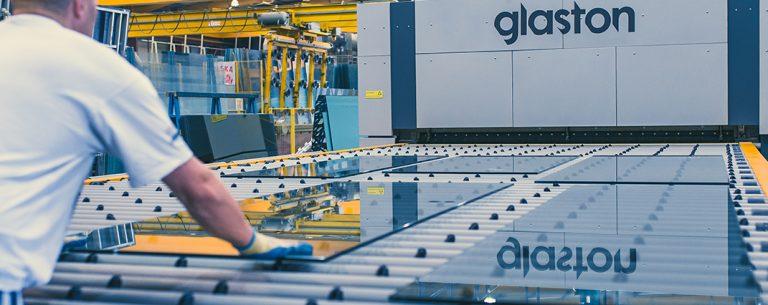
At Glaston, we are constantly developing the quality, reliability and energy efficiency of our products, because our customers’ end products require consistently higher quality and more versatile features.
Energy-efficient communities
Energy is the biggest cost item in the lifetime of buildings. Heat generation and loss through windows accounts for 25–30% of the energy used for heating and cooling buildings. New energy standards and stricter legislation are driving demand for more energy-efficient and environmentally conscious solutions in both new and renovation construction. In addition, supranational programs such as the EU’s Green Deal and campaigns such as Renovate Europe, for example, are steering societies towards more environmentally-friendly and energy-efficient solutions.
The energy-saving potential is enormous, because in the EU area up to 86% of buildings’ glass surfaces consist of outdated and less energy-efficient single or double glazing. The glass processing industry has actively developed types of glass that can be used to optimize the need for heating and cooling in buildings and thereby reduce energy consumption.
Glaston provides engineering and consulting services for the production of smart glass and energy glass windows. Demand for solar energy is growing, and strict quality requirements, for example in relation to glass thickness and curved surfaces, are set for the glass used in solar panels and cells. In smart glass applications, windows that react to fluctuations in light or temperature, for example, improve the energy performance of buildings.
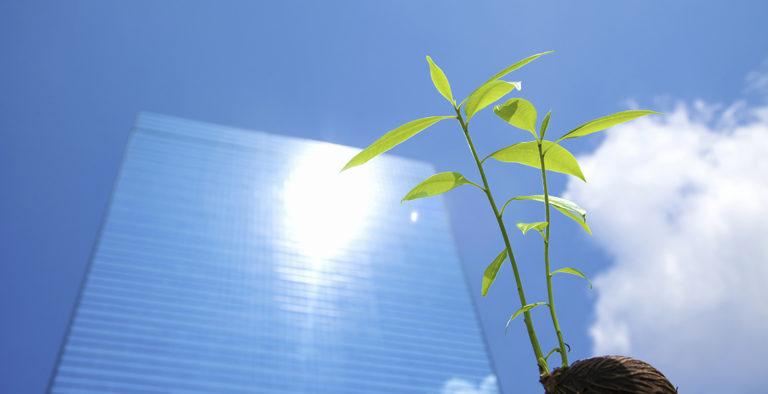
A study, published in May 2019, commissioned by Glass for Europe, finds that nearly 30% of Europe’s building energy consumption for heating and cooling could be saved in 2030 if all Europe’s buildings were equipped with high-performance glazing.
Articles
GPD 2023 Presentations – Sustainability and trends
The Glass Performance Days 2023 conference brought forward a compelling array of presentations focused on sustainability and emerging trends within the glass industry....
Read moreUnlocking energy efficiency potential: vacuum-insulated glazing for sustainable buildings
Do you know that uplifting existing building stock with high-performance insulating windows will decrease the building sector’s total energy consumption by 40%...
Read moreAeroShield at Step Change 2023 event
AeroShield makes the world’s most transparent silica aerogels. Silica aerogel is a super-insulating material. And our innovation was making it transparent...
Read more