When Semcoglas added the german Aschaffenburg location to its Company Group in October 2003, the production facility only had an old glass cutting facility and a small insulating glass line at its disposal. Since the start of this year, Semcoglas has now been working with an ultra-modern Bystronic glass production line for the manufacture of insulating glass which uses glass supplied by a rapid HEGLA glass feed system.
The new insulating glass line measures 64 metres in length and processes glass sizes ranging from 19 x 35 centimetres up to 2.70 x 5.00 metres. In doing so, the production is completely focused on the current and future requirements of the insulating glass customers. The Company Group produces insulating glass in 15 of the 20 branches and has used Bystronic glass production lines for many years – mostly including the tps’applicator for the processing of thermoplastic spacers. “We made the conscious decision to invest in this future-oriented technology as it is one of the most advanced warm edge technologies on the market: The thermoplastic edge bond simultaneously replaces a conventional metallic spacer, the desiccant and the primary seal”, explains Michel Schüller, Technical Branch Manager in Aschaffenburg and son of the Managing Partner of the Semcoglas Group, Hermann Schüller. He goes on to explain: “As a result, the thermal bridges found at the edge of the insulating glass are considerably reduced compared to the conventional spacers, thus improving the internal temperature.”
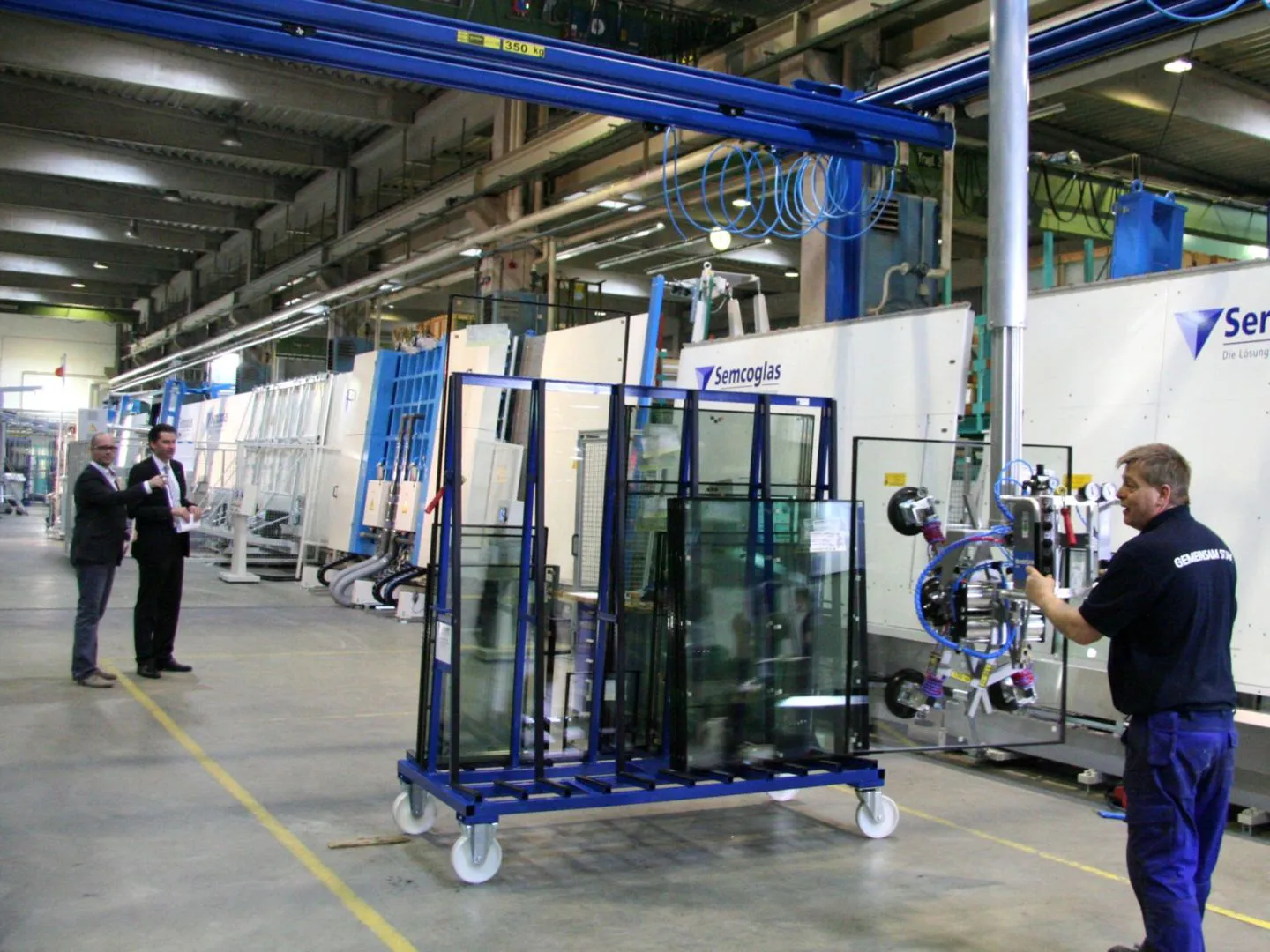
Premium insulating glass of the warm edge generation
Michel Schüller sees many benefits in thermoplastic spacers: The tps’line, which is the production line for the manufacture of insulating glass with thermoplastic spacers, offers an individual system solution for all types of orders with a unique versatility. The spacers are applied onto the glass directly by the machine from a single drum during the insulating glass production process. The width of the spacer can be individually changed as required and the stockpiling of spacers with different widths and the separate production processes for the sawing, bending, connecting, desiccant filling and butyling are no longer required.
Semcoglas annually produces more than 160,000 square metres of insulating glass in Aschaffenburg alone and intends to further expand continually. 40 percent of the insulating glasses leave the hall as triple units, with Michel Schüller noticing that the new production line can easily accommodate the significant increase in demand without any problems. The Bystronic glass tps’line in Aschaffenburg is ideally designed for the production of triple insulating glass units: In addition to the tps’applicator, this facility includes a rotating conveyor for coated glass, a tandem press for the simultaneous assembling, gas-filling and pressing of two insulating glass units as well as the fast speed’sealer sealing machine. “The use of thermoplastic spacers is of particular benefit when producing triple insulating glass units as both spacers are automatically applied without any offset whatsoever – even when dealing with shaped formats. As a result, we are able to achieve better quality even in terms of visual appearance. Semcoglas customers also appreciate this”, reports Michel Schüller. The insulating glass line is rounded off with a lightweight craneway and an Easy-Lift handling device complete with a rigid lifting column that even makes the dropping off of large and heavy insulating glass units easy.
An edge in technology, quality and service
In addition to the described technological advancements and the excellent quality of the end products, there are yet more reasons to purchase machines and units from Bystronic glass as Michel Schüller explains: “I consider the service quality to be one of the main advantages: Close co-operation with the customer – both intellectually and physically – is clearly important with the Bystronic glass team always readily available. As a customer, the Bystronic glass service department were easily attainable without any problems. The team responds extremely quickly, even regarding unexpected matters.” In addition to this, he states how easy it is for the Semcogla team to operate the plant: Thanks to the visual display on the monitors, the setting and control of the plant is almost subconsciously managed.
Website:
www.semcoglas.com