HYPERFEX Grinding Solutions
New. Improved. HYPERFEX.
The revolution in edge grinding
1.
HIGHEST GRINDING CAPACITY
2.
HIGHEST GRINDING QUALITY
3.
HIGHEST PROCESS RELIABILITY
HYPERFEX Grinding System
HYPERFEX is a new holistic approach taking into account all process relevant parameters. In combination with the HYPERFEX Administrator software, which pioneers the communication between grinding wheel and control system, there are opening up huge improvement potentials:
- Cycle time and machine performance
- Grinding quality
- Grinding wheel life time
In focus so far:
Grinding wheel only
In focus at Glaston:
The entire process
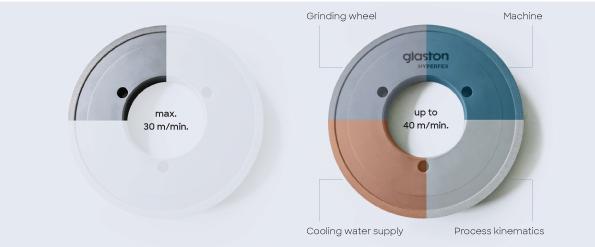
Until now, grinding wheels have been developed by manufacturers without a view of the overall process. There are however multiple important factors interacting with each other, to be considered to achieve a perfect grinding result. The grinding wheel as such needs to fit perfectly like a puzzle to all these factors.
In a project lasting several years, Glaston has developed its own grinding wheels in cooperation with experts and research institutions.
Our individually composed grinding wheels are the perfect match to comply with all application quirements.
Aspects of the overall process are
- Cutting- and breaking process, grinding allowance
- Stiffness and vibration behaviour of the construction elements
- Wear condition of the machine
- Repetition accuracy of the CNC axes
- Optimized speed and acceleration of all machine axes
- Coolant system and fluid technology of the nozzle rings
- Specific customer quality requirements
- Machine generation and upgrade possibilities to latest ACS
The new product family
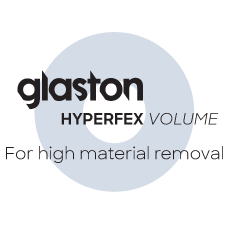
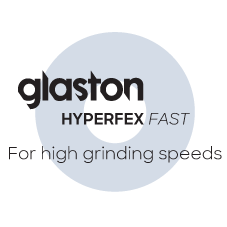
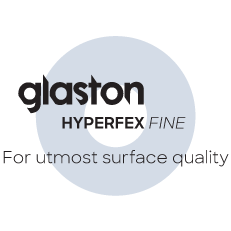
Depending on application and process, the use of VOLUME, FAST or FINE grinding wheels will lead to the best possible result.
Technical background:
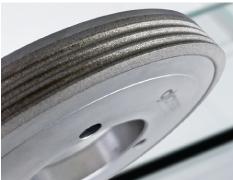
Multigroove grinding wheels
- High-precision Z-axis adjustment on all Glaston machines as a precondition
- The HYPERFEX Administrator software enables the communication between grinding wheel and control system to easily handle up to 10 grooves in one wheel
- Huge potential in improved efficiency
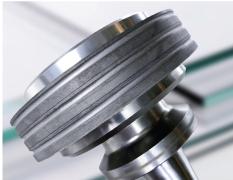
Grinding wheels with different compositions as sandwich
- High-precision Z-axis adjustment on all Glaston machines as a precondition
- The Multi Grinding software enables repeated grinding cycles with up to three grinding wheels of different compositions
- Customized wheel compositions ensure grinding results close to polishing
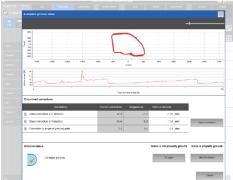
Glaston digital services
- Subscription based Insight Automotive PLUS:
Saves approx. 20 min. time for each model change without any piece of scrap - Subscription based Insight Automotive PRO:
Self adjusting machine parameters based on constant grinding process monitoring - Automatic tool break-in for new and re-profiled tools
- All Glaston digital services can be retrofitted as an upgrade for machines from 2010 onwards
References
FLACHGLAS, Germany
#flat glass laminating #glass processing #glass quality #laminated glass #laminating #ProL #ProL-zone #quality control #reference #safety glass #upgrades
At FLACHGLAS, a culture of operational excellence fuels continuous modernizations. “The latest Glaston ProL upgrade for our 50-year-old lamination line has helped us raise performance, save energy and automate production with the push of a button,” says Martin Geiss, Technical Manager at FLACHGLAS Wernberg.
Read moreLippert Components, USA
#automation #automotive #automotive glass #bending #CHAMP #CHF #glass bending #glass tempering #Matrix #reference #safety glass
Tim Widner at Lippert Components in the US is sharing his and his team's experiences working with the Glaston glass processing machinery. "The new equipment has been a great addition to us. We are able to one-piece flow our raw material through our line, hands-free. No humans come in contact with the glass until it is fully tempered and at the end of the process."
Read morePress Glass Inc., U.S.A.
#automation #flat glass laminating #glass processing #laminating #ProL #reference #safety glass #upgrades
Since establishing their presence in the US through an acquisition, Poland-based Press Glass has continued its brisk growth based on the same values that make it the #1 glass fabricator in Europe and the UK. The company’s latest US investment is a Glaston ProL convection control upgrade at its Ridgeway, Virginia, plant.
Read moreArticles
GPD 2023 Presentations – Sustainability and trends
The Glass Performance Days 2023 conference brought forward a compelling array of presentations focused on sustainability and emerging trends within the glass industry....
Read moreGPD 2023 Presentations – Glass processing technologies
The Glass Performance Days 2023 conference showcased a range of pioneering presentations on glass processing technologies, bringing together industry leaders and...
Read moreGPD 2023 Presentations – Architectural glass
The Glass Performance Days 2023 conference has once again brought together a wealth of knowledge and innovation from the leading minds in the glass industry. We...
Read more