IKU – De-airing conveyor
Here are three reasons for choosing IKU
1.
High performance
- Efficient air removal by the vacuum ring method
- Effective convection heating with uniform and controlled air flow distribution
- High capacity for both windscreen and sidelite production
2.
Flexible versatility
- All windscreen sizes on the market
- Wide range of capacity levels
- Efficient floor space utilization with a vertical glass processing position
3.
Proven reliability
- Proven technology based on decades-long product development
- Market leader in de-airing laminated glass
- Comprehensive Glaston services over the lifetime of your machinery
Enhanced de-airing by efficient air removal and heating
With over 50 years of experience in heat treatment technology, Glaston has developed a high-quality solution for de-airing of laminated glass.
The new Glaston IKU semi-continuous de-airing conveyor incorporates proven technology for effective air removal as well as uniform heating for your enhanced de-airing results.
IKU covers all windscreen sizes on the market and a wide range of capacity levels, while enabling various layout possibilities for your tailored processing needs.
IKU is suitable for both windscreen and laminated sidelites production of high capacity.
References
FLACHGLAS, Germany
#flat glass laminating #glass processing #glass quality #laminated glass #laminating #ProL #ProL-zone #quality control #reference #safety glass #upgrades
At FLACHGLAS, a culture of operational excellence fuels continuous modernizations. “The latest Glaston ProL upgrade for our 50-year-old lamination line has helped us raise performance, save energy and automate production with the push of a button,” says Martin Geiss, Technical Manager at FLACHGLAS Wernberg.
Read morePress Glass Inc., U.S.A.
#automation #flat glass laminating #glass processing #laminating #ProL #reference #safety glass #upgrades
Since establishing their presence in the US through an acquisition, Poland-based Press Glass has continued its brisk growth based on the same values that make it the #1 glass fabricator in Europe and the UK. The company’s latest US investment is a Glaston ProL convection control upgrade at its Ridgeway, Virginia, plant.
Read moreConsolidated Glass Corporation, U.S.A.
#appliances #architectural #automation #flat glass laminating #laminating #ProL #reference #safety glass
“We saw the move into laminating glass as an exciting opportunity to explore. It gives us an open door to many new areas, such as security, acoustic and decorative glass. After thoroughly reviewing six lines, we chose Glaston’s ProL lamination thanks to its convection heating and simplicity,” say Consolidated Glass Corporation’s Brad Bartley, General Manager, and Lindsey Merryman, Lamination Line Program Manager.
Read moreContact information
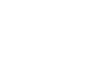