ScreenMax
A superior solution for bending large high-quality windshields
Looking to produce large high-quality windshields?
Here are three reasons why Glaston ScreenMax is your best choice
1.
#1 choice for OEM and ARG bus windshield production
- The world’s most trusted solution
- Used by the top windshield producers
- Made in Finland from engineering to production
2.
Processes the most complicated shapes
- Ultimate heating control with grooved heaters
- Advanced mold technology
- Over 50 years of process expertise
3.
Start small, dream big
- Easy to upgrade and stay at the top of the market
- Modular construction allows capacity to grow
- Automated processing features for more complex production
Flexible bending performance for serial and mixed production
ScreenMax is designed for the serial bending of large bus windshields. ScreenMax is the smart, long-term choice for both OEMs and ARGs. It is the #1 choice for top bus windshield producers in the world. ScreenMax is made in Finland from engineering to production, backed by our team with 50+ years of process expertise.
Our groove-fitted heaters, together with ultimate heating control, guarantee superior and accurate shape control.
Built-in processing features, such as automated middle support and wing triggering systems, ensure the highest quality, regardless of production scale. These features also allow us to increase the automation of your business.
ScreenMax’s modular design gives you the flexibility to produce any size and shape of windshields you require. Choose from a selection of capability options, wagon sizes and furnace lengths to fit your production conditions. This design allows easy expansion and customization, as your production needs evolve. Regular software and technological upgrades also ensure that your machine remains safe and efficient.
References
Euroglas, Belgium
#flat glass tempering #glass tempering #iControL #RHC #safety glass #tempered glass #upgrades
Euroglas chose Glaston’s Roller Heat Control (RHC) upgrade to improve its tempering line performance as part of a series of investments to grow with its customers. “We aim to offer the width and depth of glass products they need to be their best partner,” says Frederik De Knijf, CEO of Euroglas in Belgium.
Read morePilkington Automotive Finland, Finland
#automotive glass #automotiveindustry #CNC #CNC96 #lifecycleservices #mobility #reference #upgrades
“We decided to extend the lifetime of our Bystronic (now Glaston) automotive glass cutting equipment with a Glaston CNC96 upgrade kit and ensure that we can continue to get spare parts,” says Matti Säynäväjärvi, Technical Services Group Leader, Pilkington Automotive Finland Oy, Laitila plant.
Read moreViridian Glass, Australia
#architectural #automation #COMFORT #glass quality #IG unit #insulating glass #reference
As building regulations require more energy-efficient glass, Viridian Glass has stepped up its game. Purchasing Glaston’s COMFORT BOX IG manufacturing line enables its Woodville plant in Adelaide to meet burgeoning demands with visibly better quality and shorter lead times. “High quality insulated glass is the future in Australia,” says, National Operational Excellence Manager, Tarun Bhatia at Viridian Glass.
Read moreArticles
GPD 2023 Presentations – Research and development
The Glass Performance Days 2023 conference featured a wealth of cutting-edge research and development sessions. This category is dedicated to showcasing groundbreaking...
Read moreSolving windscreen and sunroof production issues with convection preheating
The complexity of automotive windshields and sunroofs has significantly increased with evolving modern car designs. Achieving uniform heating for such complex glass...
Read moreEnergy efficiency best practices in automotive glass production
In this blog, we share some practical tips for optimizing energy consumption in automotive glass production. From preprocessing to final inspection, there is huge...
Read moreContact information
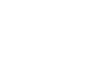