Automatic sealing
Continuous sealing of insulating glass units with different forms and dimensions
Here are three reasons why Glaston’s automatic sealing solution is your best choice
1.
Continuous, automatic sealing of insulating glass units in varying forms and dimensions
2.
Fast, volume-controlled dosing system
3.
Excellent mixing and dosing quality
ACTIVE’SEALER
Convincing gear pump dosing technology matters
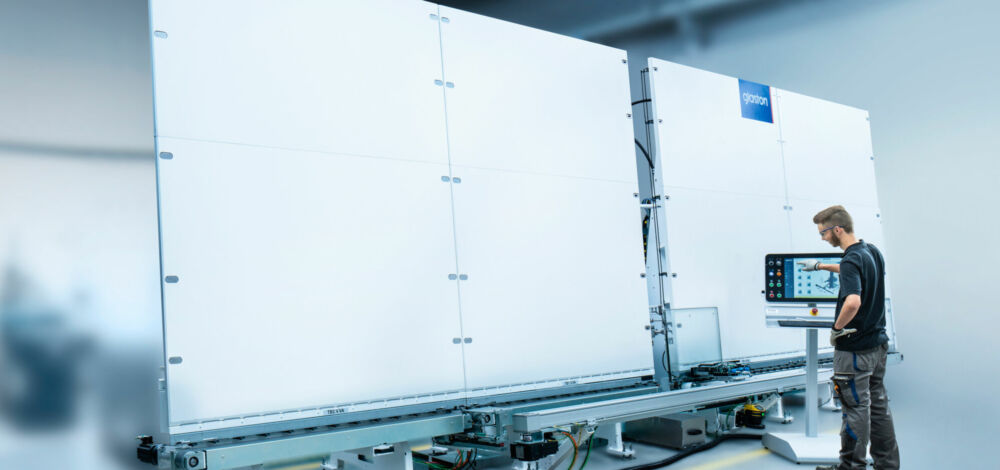
Glaston‘s new automatic sealing robot ACTIVE‘SEALER is an ideal solution for the automated sealing process of double and triple insulating glass units.
- Excellent mixing and dosing quality for all approved two-component sealants
- Convincing gear pump system ensures a high material dosing accuracy
- Excellent sealing quality due to volumecontrolled dosing system close to the nozzle
- The mixing ratio is electronically adjustable
- Automatic nozzle centering for varying spacer widths
- Homogeneously sealed corners due to nozzlespatula system
- Safe and clean glass transport due to air cushions and a conveyor system consisting
of individual belts with integrated, easily exchangeable support bars - Easy to use human machine interface with an intuitive touch screen display
SPEED’SEALER
High-speed sealing robot for insulating glass units
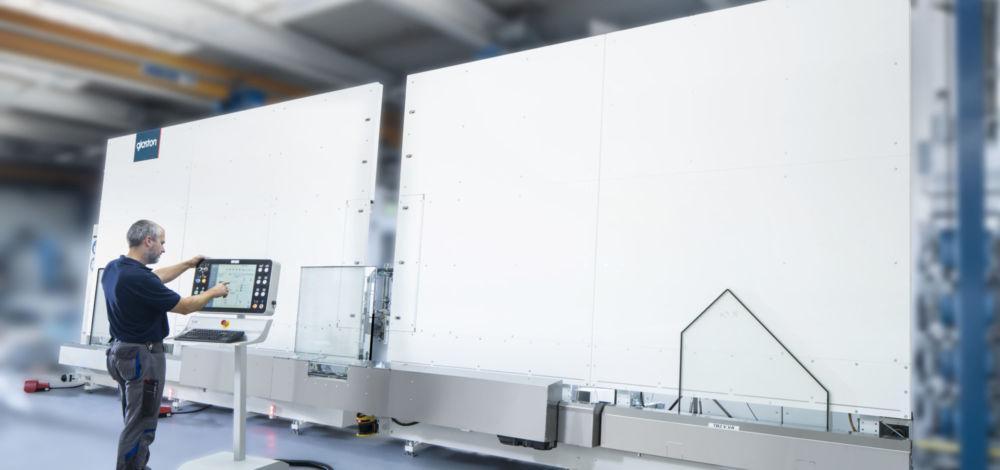
Slow was yesterday
With SPEED’SEALER, you can really step on the gas
- Highly accurate dosing technology for instant volume adjustment when there are changes in the joint depth
- Optimum sealing quality, even with changes in temperature and material batch as well as at the start of production
- Self-monitoring, constant mixing ratio of the two material components
- Self-cleaning, flow-optimized mixer prevents clogging in the mixing section
- Reduced wear and tear due to very low fluid pressure
- Graphical user interface for intuitive control through a touchscreen
XXL’SEALER
Sealing technology with new dimensions
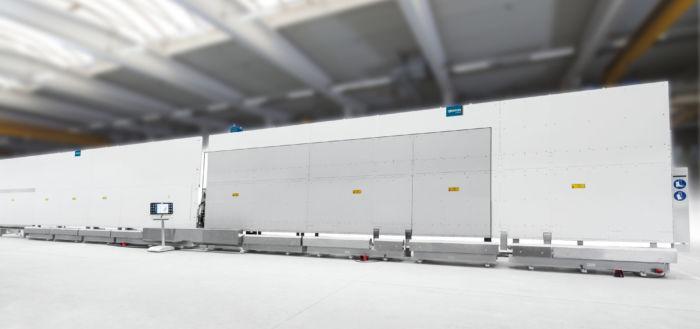
Automatic sealing of the highest level
The solution for maximum requirements
- Continuous, automatic sealing of insulating glass units with different forms and dimensions, especially suitable for large-dimensioned elements up to 18 m in length (XXL version)
- Homogeneously sealed corners due to the nozzle/spatula system
- Patented conveyor systems for safe and clean transport
- Modular engineering concept
Options
- Automatic sealing of up to four-sided stepped insulating glass units
- Automatic sealing material changing system – up to 10 times faster than other systems
- 200-liter drum pump for B component
- Several undergrip options available in the discharge area
- Nozzles for special applications
References
Pilkington Automotive Finland, Finland
#automotive glass #automotiveindustry #CNC #CNC96 #lifecycleservices #mobility #reference #upgrades
“We decided to extend the lifetime of our Bystronic (now Glaston) automotive glass cutting equipment with a Glaston CNC96 upgrade kit and ensure that we can continue to get spare parts,” says Matti Säynäväjärvi, Technical Services Group Leader, Pilkington Automotive Finland Oy, Laitila plant.
Read moreViridian Glass, Australia
#architectural #automation #COMFORT #glass quality #IG unit #insulating glass #reference
As building regulations require more energy-efficient glass, Viridian Glass has stepped up its game. Purchasing Glaston’s COMFORT BOX IG manufacturing line enables its Woodville plant in Adelaide to meet burgeoning demands with visibly better quality and shorter lead times. “High quality insulated glass is the future in Australia,” says, National Operational Excellence Manager, Tarun Bhatia at Viridian Glass.
Read moreAGP, New Zealand
#architectural #automation #autopilot #digitalization #FC Series #flat glass tempering #reference
“We’re now running with the stability, reliability and consistency we aimed to achieve when we invested in Glaston’s Autopilot,” David Bunting, Managing Director of Architectural Glass Products (AGP), says.
Read moreArticles
Breakthroughs in automating glass processing
From traditional applications to cutting-edge capabilities, automation revolutionizes production, enhances quality and boosts efficiency. In this blog, we’ll discuss...
Read moreKey takeaways from glasstec 2024
Held in late October, glasstec 2024 buzzed with energy, robotic solutions and serious discussions. Based on what we saw and heard at the event, we can outline a...
Read moreKey applications of automation in glass processing
What glass processes gain the most from automation? In this blog, we’ll focus on some of the particularly promising application areas. As we discovered in the...
Read moreContact information
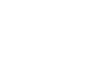
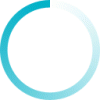