Spacer filling
Manual or automatic spacer filling in shortest cycle times
Here are three reasons why Glaston’s spacer filling solution is your best choice
1.
Simplified logistics using the first-in/first-out process
2.
Processing of different types of spacer frames
3.
Parallel filling and transporting operations
SPACER’FILLER M
Desiccant filling station for subsequent filling
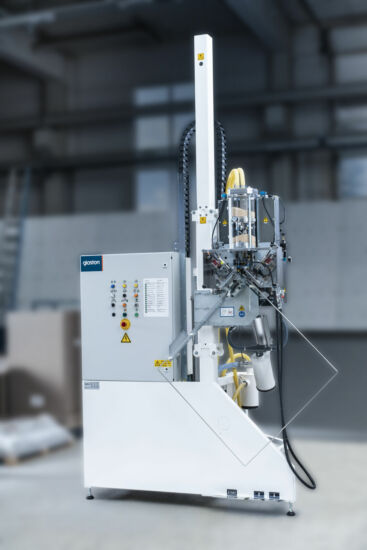
- Drilling, filling and sealing of two frame members simultaneously
- Sensor-controlled monitoring of the filling process guarantees an optimum filling degree
- Desiccant feeding by 200-liter big bags
- Removal of excessive desiccant grains by suction
- Automatic sealing of the filling holes with butyl
- Feeding unit can be infinitely adjusted pneumatically
SPACER’FILLER AT
Desiccant filling without manual intervention provides the shortest cycle times thanks to parallel filling and transporting operations
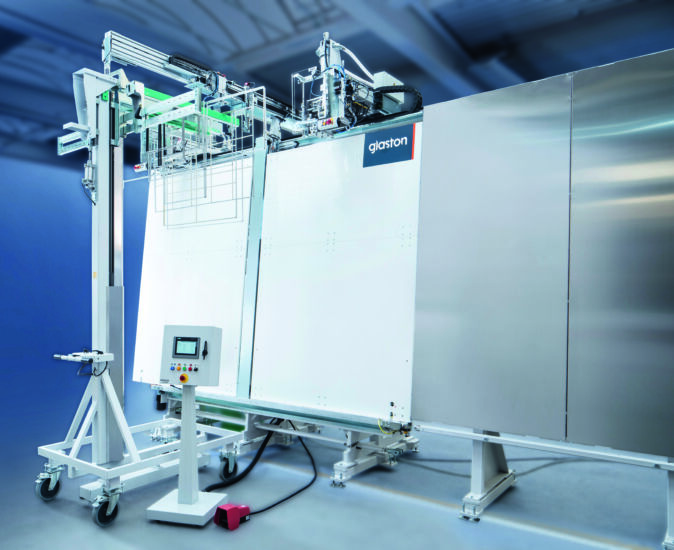
- Simplified logistics using the first-in/first-out process
- Processing of stretched and curved frames made of aluminum, steel, stainless steel or plastic profiles
- Proven drilling of the fill holes centered at the back of the spacer profile
- Parallel drilling and filling of the two vertical frame legs
- Clean and sensor-controlled filling operation with removal of excessive desiccant grains by suction
- Spherical, desiccant grains with a diameter from 0.5–0.9 mm (0.02–0.04 in), 200-liter (55-gallon) drums
- Automatic butyl sealing of the filling holes
- Automatic frame transfer to the SPACER’BUTYLAPPLICATOR
- Processing symmetrical internal bars up to 40 mm (1.57 in) wide
- Shape filling in manual operation possible
Options
- Picker – frame carrier for spacer frame buffering at spacerbending machines
- Feeder – frame carrier for spacer frame buffering and transportation from spacerbending machines to the SPACER’FILLER AT
References
Pilkington Automotive Finland, Finland
#automotive glass #automotiveindustry #CNC #CNC96 #lifecycleservices #mobility #reference #upgrades
“We decided to extend the lifetime of our Bystronic (now Glaston) automotive glass cutting equipment with a Glaston CNC96 upgrade kit and ensure that we can continue to get spare parts,” says Matti Säynäväjärvi, Technical Services Group Leader, Pilkington Automotive Finland Oy, Laitila plant.
Read moreViridian Glass, Australia
#architectural #automation #COMFORT #glass quality #IG unit #insulating glass #reference
As building regulations require more energy-efficient glass, Viridian Glass has stepped up its game. Purchasing Glaston’s COMFORT BOX IG manufacturing line enables its Woodville plant in Adelaide to meet burgeoning demands with visibly better quality and shorter lead times. “High quality insulated glass is the future in Australia,” says, National Operational Excellence Manager, Tarun Bhatia at Viridian Glass.
Read moreAGP, New Zealand
#architectural #automation #autopilot #digitalization #FC Series #flat glass tempering #reference
“We’re now running with the stability, reliability and consistency we aimed to achieve when we invested in Glaston’s Autopilot,” David Bunting, Managing Director of Architectural Glass Products (AGP), says.
Read moreArticles
Breakthroughs in automating glass processing
From traditional applications to cutting-edge capabilities, automation revolutionizes production, enhances quality and boosts efficiency. In this blog, we’ll discuss...
Read moreKey takeaways from glasstec 2024
Held in late October, glasstec 2024 buzzed with energy, robotic solutions and serious discussions. Based on what we saw and heard at the event, we can outline a...
Read moreKey applications of automation in glass processing
What glass processes gain the most from automation? In this blog, we’ll focus on some of the particularly promising application areas. As we discovered in the...
Read moreContact information
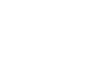