VARIO
The system solution for insulating glass using conventional, flexible and TPS® - Thermo Plastic Spacer
Looking for an individually configurable insulating glass production line?
Here are three reasons why Glaston VARIO is your best choice
1.
High flexibility and excellent productivity
2.
Long service life WITH PREMIUM COMPONENTS
3.
Multiple line expansion options
The insulating glass line Glaston VARIO is an individually configurable production line for insulating glass unit manufacturing. It is available in the following variants:
VARIO BOX
Individually configurable production line for insulating glass units with conventional spacers.
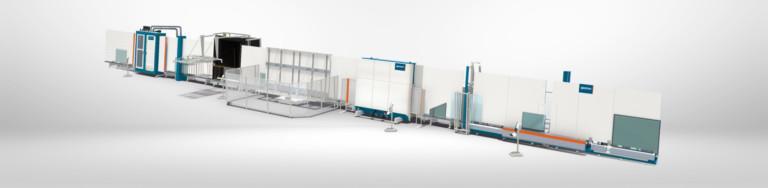
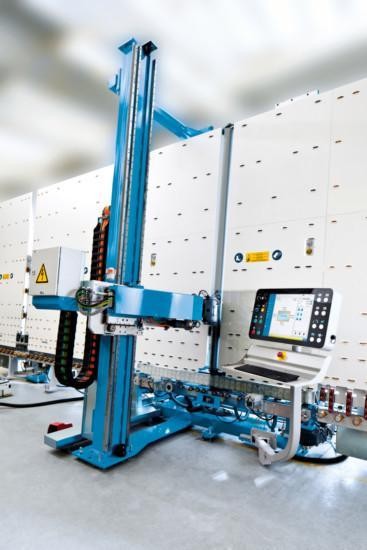
Coated glass plate edge deletion
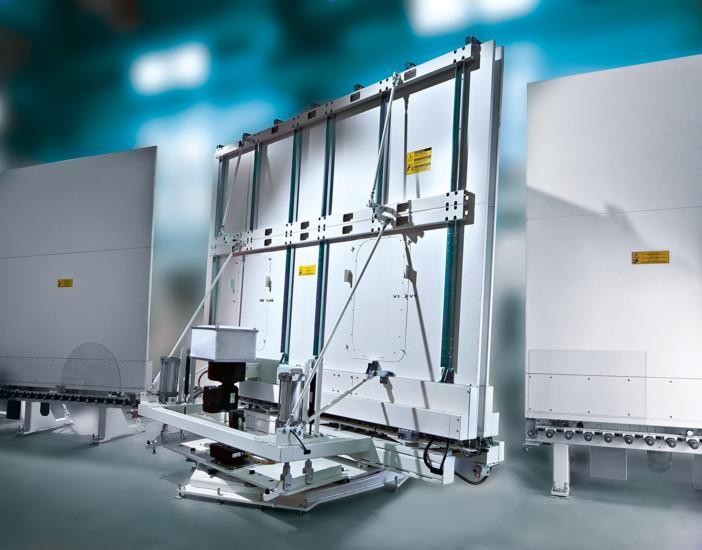
Automatic turning of coated glass plates within an insulating glass line
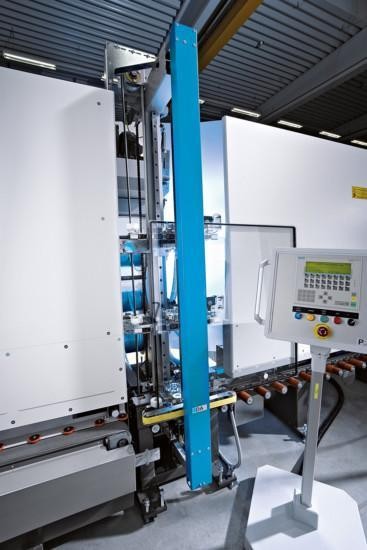
Application of pre-punched spacer pads on insulating glass units
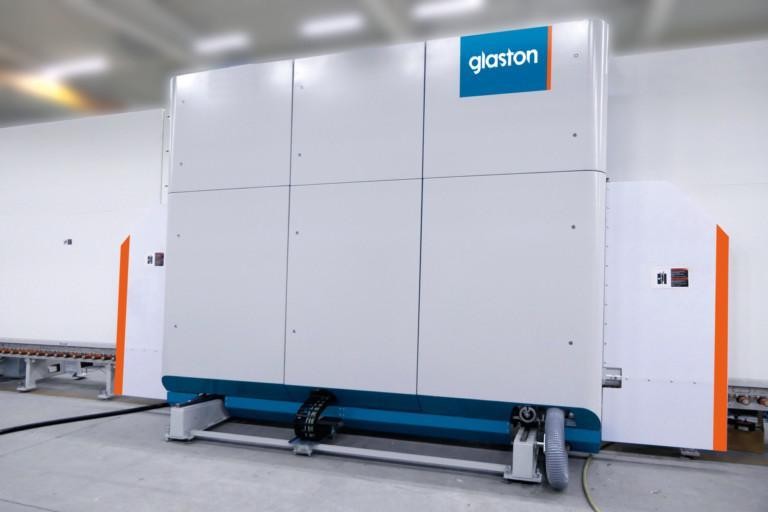
Automatic assembling, gas filling and pressing, especially for triple insulating glass units
VARIO FLEX
Individually configurable production line for insulating glass units with flexible spacers from the reel.
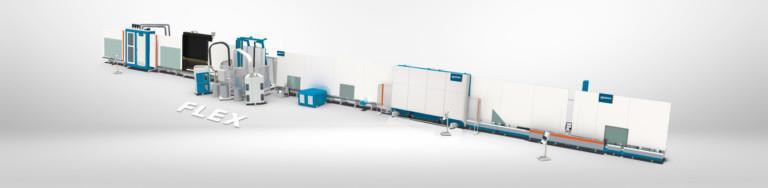
The insulating glass line Glaston VARIO FLEX offers a solution for the automatic production of gas-filled and sealed insulating glass units incorporating flexible warm edge spacers.
- Synchronized spacer application with the insulating glass manufacturing process
- Production sequence of rectangular and shaped formats as desired
- Direct flexible spacer application onto the vertically positioned glass plate
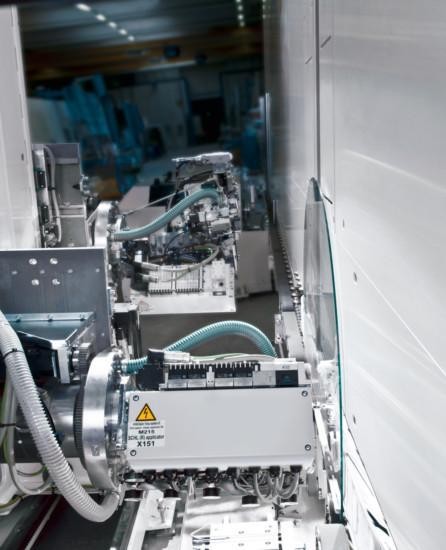
Twin-head applicator for interruption-free insulating glass unit production with different spacer widths
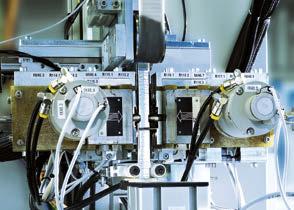
Processing of flexible spacers with double-sided polyisobutylene application
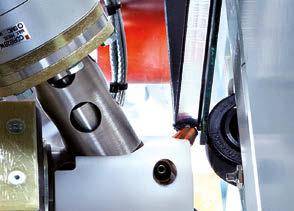
Secure corner sealing fixed using tape strips and additional butyl sealant
VARIO TPS®
Individually configurable production line for insulating glass units with TPS® Thermo Plastic Spacer.
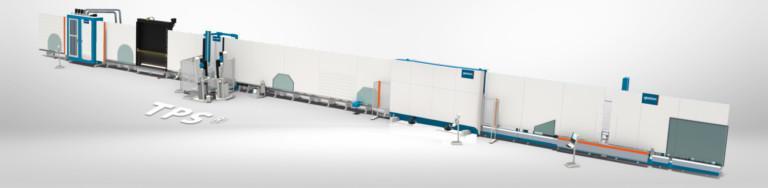
The insulating glass line Glaston VARIO TPS® offers a unique, versatile and individual production solution for all types of orders. It differs from the conventional production systems by the direct application of the TPS® Thermo Plastic Spacer onto the glass plate.
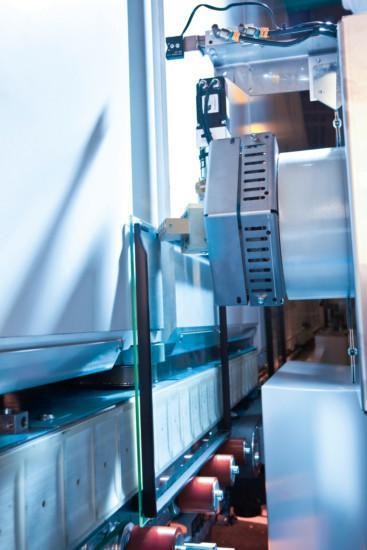
Direct application of the Thermo Plastic Spacer (TPS®) onto the glass plate. The spacer width can be changed as desired during operation without any time loss.
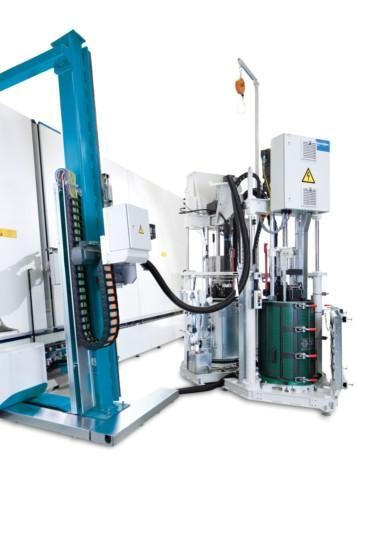
The dual-drum pump system enables completely interruption-free operation.
The material drum change takes place during production.
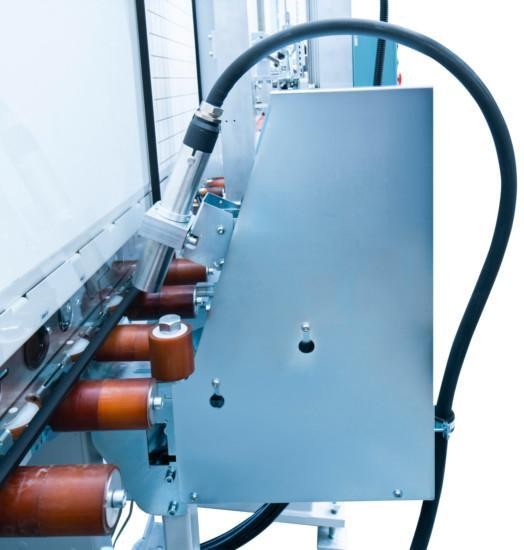
Possibility of individual product identification according to local regulations.
References
Glas Dreisbusch, Germany
#architectural #IG unit #insulating glass #TPS #VARIO
“The idea of a special U-shaped design to fit our confined space was created over lunch by my son Maximillian Dreisbusch and two Glaston service engineers. I think this says everything about our close and collaborative partnership with Glaston,” says Thomas Dreisbusch, Managing Director of Glas Dreisbusch.
Read moreNortheast Building Products, U.S.A.
#architectural #glass processing #IG unit #insulating glass #reference #TPS #VARIO
With over 650 employees, Northeast Building Products, based in Philadelphia PA, USA, manufactures high quality, energy efficient windows, doors and ancillary products for the residential window and door market. Alan Levin, President of NBP, has partnered with Bystronic glass since 2009 when they invested in the cutting edge Sashlite™ technology, SashLine, to support the company’s diversification and growth strategy.
Read moreLerobel, Belgium
#architectural #glass processing #IG unit #insulating glass #TPS #VARIO
Standard insulating glass is now a thing of the past; the Lerobel Company is breaking new ground, and in the process astonishing even experienced Bystronic glass sales engineers. Company owner Yannick Leroi and his project manager Rudi Vaneyck discuss the co-operation with Bystronic glass and why they have placed their trust in the TPS-4SG technology through a substantial investment.
Read moreArticles
The rise of thin triple insulating glass units: An industry game-changer
The push for better thermal performance in insulating glass units (IGUs) is greater than ever. For example, the 2024 Energy Star guidelines in the U.S. have set...
Read moreGPD 2023 Presentations – Sustainability and trends
The Glass Performance Days 2023 conference brought forward a compelling array of presentations focused on sustainability and emerging trends within the glass industry....
Read moreGPD 2023 Presentations – Architectural glass
The Glass Performance Days 2023 conference has once again brought together a wealth of knowledge and innovation from the leading minds in the glass industry. We...
Read moreContact information
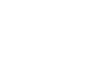